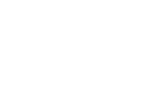
Our highly trained in house electrical technicians specialize in electrical maintenance, repairs, and installations.
Electrical Panel Repair and Refurbishment
Industrial and mining electrical panel repair and refurbishment involve the inspection, maintenance, repair, and upgrade of electrical control panels used in industrial and mining applications. Electrical panels, also known as switchboards or control panels, play a central role in controlling and distributing electrical power to various equipment and machinery within industrial and mining facilities.
Over time, these panels may experience wear, aging, or malfunctions, necessitating repair and refurbishment to ensure their continued reliability and safety. Industrial and mining electrical panel repair and refurbishment are critical for maintaining the reliability, safety, and efficiency of electrical distribution systems in these demanding environments.
Professional electrical technicians or engineers with expertise in industrial and mining electrical systems typically perform these tasks to ensure compliance with industry standards and regulations.
Key aspects of industrial and mining electrical panel repair and refurbishment include
Inspection and Assessment
A thorough inspection is conducted to assess the condition of the electrical panel. This includes checking for signs of wear, corrosion, loose connections, damaged components, and compliance with safety standards.
Cleaning and Decontamination
Industrial environments, especially in mining, can expose electrical panels to dust, dirt, and contaminants. Cleaning and decontamination are essential to prevent issues such as electrical arcing and ensure proper heat dissipation.
Rewiring and Cable Replacement
If wiring or cables show signs of damage or deterioration, they are replaced to maintain electrical integrity and prevent the risk of short circuits or electrical faults.
Compliance with Regulations
Industrial and mining electrical panels must comply with relevant safety and electrical codes and standards. During refurbishment, any necessary modifications are made to ensure compliance with the latest regulations.
Labeling and Documentation
Proper labeling of components and circuits is essential for maintenance and troubleshooting. Updated documentation is provided to reflect any changes made during the repair and refurbishment process.
Safety Measures
Safety features, such as emergency stops, warning labels, and interlocks, are verified and, if necessary, upgraded to ensure the safety of personnel working with or near the electrical panel.
Testing and Diagnostics
Various electrical tests are performed to identify any issues with components, circuits, and overall functionality. This may include insulation resistance testing, continuity checks, and verifying the accuracy of meters and gauges.
Upgrades and Modernization
Refurbishment may include upgrading the electrical panel with modern components or technologies to enhance functionality, efficiency, and safety. This could involve adding new control features, digital meters, or communication interfaces.
Replacement of Components
Worn-out or damaged components, such as circuit breakers, contactors, relays, and meters, are replaced with new ones to maintain the reliability and performance of the electrical panel.
Sealing and Environmental Protection
In mining environments, electrical panels may be exposed to moisture and harsh conditions. Sealing measures and environmental protection measures, such as the use of NEMA or IP enclosures, are implemented to safeguard the panel against these elements.
Functional Testing
After repairs and refurbishment, the electrical panel undergoes functional testing to ensure that all components work as intended and that the panel can effectively control and distribute electrical power.
Electrical Panel Design and
Assembly
Industrial and mining electrical panel design and assembly involve the planning, engineering, and construction of electrical control panels used in industrial and mining applications. These panels, also known as switchboards or control boards, serve as central hubs for controlling and distributing electrical power to various equipment and machinery within industrial and mining facilities.
The design and assembly process ensures that the electrical panels are configured to meet specific operational requirements, safety standards, and environmental conditions of industrial and mining environments. Industrial and mining electrical panel design and assembly demand a collaborative effort involving electrical engineers, designers, and skilled technicians.
The goal is to create a reliable, efficient, and safe electrical distribution system tailored to the specific needs and challenges of industrial and mining applications.
Key aspects of industrial and mining electrical panel repair and refurbishment include
Needs Assessment
A thorough assessment is conducted to understand the electrical requirements and operational needs of the industrial or mining facility. This includes determining the voltage levels, power distribution requirements, control systems, and safety considerations.
System Architecture
Engineers develop a system architecture that outlines the arrangement of components, control devices, and power distribution within the electrical panel. This includes considerations for the layout and organization of the panel’s interior.
Wiring Diagrams and Schematics
Creation of detailed wiring diagrams and schematics that illustrate the electrical connections, circuits, and relationships between components. These diagrams serve as a guide during the assembly process and for future troubleshooting.
Safety Features
Incorporation of safety features is a priority, including emergency stops, interlocks, fault protection, and other measures to safeguard personnel and equipment.
Cable Management
Efficient cable routing and management are crucial for preventing interference, reducing the risk of electrical faults, and facilitating ease of maintenance. Cable entry and exit points are carefully planned.
Testing and Quality Assurance
Rigorous testing is conducted to verify the functionality, safety features, and compliance of the assembled electrical panel. This may include electrical testing, insulation resistance tests, and functional checks.
Regulatory Compliance
Designing electrical panels involves adherence to applicable electrical codes, safety standards, and regulations governing industrial and mining installations. Compliance with local and international standards is critical for ensuring safety and reliability.
Component Selection
Selection of components such as circuit breakers, relays, contactors, switches, meters, and other devices is a crucial part of the design process. The chosen components must meet the specifications of the industrial or mining application.
Environmental Considerations
Panels in mining and industrial settings may be exposed to harsh environmental conditions. Designers consider factors like temperature extremes, humidity, dust, and corrosive substances, selecting components and enclosures that can withstand these conditions.
Panel Enclosure
Selection of an appropriate enclosure (NEMA or IP rated) based on the environmental conditions to protect the panel from external elements such as water, dust, and chemicals.
Assembly and Wiring
Skilled technicians assemble the electrical panel, following the design specifications. Wiring is carefully executed to ensure proper connections, reduce electromagnetic interference, and maintain electrical integrity.
Documentation
Comprehensive documentation, including operation manuals, maintenance procedures, and as-built drawings, is prepared for future reference.
Electrical Panel Repair and Refurbishment
Industrial and mining electrical panel repair and refurbishment involve the inspection, maintenance, repair, and upgrade of electrical control panels used in industrial and mining applications. Electrical panels, also known as switchboards or control panels, play a central role in controlling and distributing electrical power to various equipment and machinery within industrial and mining facilities.
Over time, these panels may experience wear, aging, or malfunctions, necessitating repair and refurbishment to ensure their continued reliability and safety. Industrial and mining electrical panel repair and refurbishment are critical for maintaining the reliability, safety, and efficiency of electrical distribution systems in these demanding environments.
Professional electrical technicians or engineers with expertise in industrial and mining electrical systems typically perform these tasks to ensure compliance with industry standards and regulations.
Key aspects of industrial and mining electrical panel repair and refurbishment include
Inspection and Assessment
A thorough inspection is conducted to assess the condition of the electrical panel. This includes checking for signs of wear, corrosion, loose connections, damaged components, and compliance with safety standards.
Cleaning and Decontamination
Industrial environments, especially in mining, can expose electrical panels to dust, dirt, and contaminants. Cleaning and decontamination are essential to prevent issues such as electrical arcing and ensure proper heat dissipation.
Rewiring and Cable Replacement
If wiring or cables show signs of damage or deterioration, they are replaced to maintain electrical integrity and prevent the risk of short circuits or electrical faults.
Compliance with Regulations
Industrial and mining electrical panels must comply with relevant safety and electrical codes and standards. During refurbishment, any necessary modifications are made to ensure compliance with the latest regulations.
Labeling and Documentation
Proper labeling of components and circuits is essential for maintenance and troubleshooting. Updated documentation is provided to reflect any changes made during the repair and refurbishment process.
Safety Measures
Safety features, such as emergency stops, warning labels, and interlocks, are verified and, if necessary, upgraded to ensure the safety of personnel working with or near the electrical panel.
Testing and Diagnostics
Various electrical tests are performed to identify any issues with components, circuits, and overall functionality. This may include insulation resistance testing, continuity checks, and verifying the accuracy of meters and gauges.
Upgrades and Modernization
Refurbishment may include upgrading the electrical panel with modern components or technologies to enhance functionality, efficiency, and safety. This could involve adding new control features, digital meters, or communication interfaces.
Replacement of Components
Worn-out or damaged components, such as circuit breakers, contactors, relays, and meters, are replaced with new ones to maintain the reliability and performance of the electrical panel.
Sealing and Environmental Protection
In mining environments, electrical panels may be exposed to moisture and harsh conditions. Sealing measures and environmental protection measures, such as the use of NEMA or IP enclosures, are implemented to safeguard the panel against these elements.
Functional Testing
After repairs and refurbishment, the electrical panel undergoes functional testing to ensure that all components work as intended and that the panel can effectively control and distribute electrical power.
Electrical Panel Design and
Assembly
Industrial and mining electrical panel design and assembly involve the planning, engineering, and construction of electrical control panels used in industrial and mining applications. These panels, also known as switchboards or control boards, serve as central hubs for controlling and distributing electrical power to various equipment and machinery within industrial and mining facilities.
The design and assembly process ensures that the electrical panels are configured to meet specific operational requirements, safety standards, and environmental conditions of industrial and mining environments. Industrial and mining electrical panel design and assembly demand a collaborative effort involving electrical engineers, designers, and skilled technicians.
The goal is to create a reliable, efficient, and safe electrical distribution system tailored to the specific needs and challenges of industrial and mining applications.
Key aspects of industrial and mining electrical panel repair and refurbishment include
Needs Assessment
A thorough assessment is conducted to understand the electrical requirements and operational needs of the industrial or mining facility. This includes determining the voltage levels, power distribution requirements, control systems, and safety considerations.
System Architecture
Engineers develop a system architecture that outlines the arrangement of components, control devices, and power distribution within the electrical panel. This includes considerations for the layout and organization of the panel’s interior.
Wiring Diagrams and Schematics
Creation of detailed wiring diagrams and schematics that illustrate the electrical connections, circuits, and relationships between components. These diagrams serve as a guide during the assembly process and for future troubleshooting.
Safety Features
Incorporation of safety features is a priority, including emergency stops, interlocks, fault protection, and other measures to safeguard personnel and equipment.
Cable Management
Efficient cable routing and management are crucial for preventing interference, reducing the risk of electrical faults, and facilitating ease of maintenance. Cable entry and exit points are carefully planned.
Testing and Quality Assurance
Rigorous testing is conducted to verify the functionality, safety features, and compliance of the assembled electrical panel. This may include electrical testing, insulation resistance tests, and functional checks.
Regulatory Compliance
Designing electrical panels involves adherence to applicable electrical codes, safety standards, and regulations governing industrial and mining installations. Compliance with local and international standards is critical for ensuring safety and reliability.
Component Selection
Selection of components such as circuit breakers, relays, contactors, switches, meters, and other devices is a crucial part of the design process. The chosen components must meet the specifications of the industrial or mining application.
Environmental Considerations
Panels in mining and industrial settings may be exposed to harsh environmental conditions. Designers consider factors like temperature extremes, humidity, dust, and corrosive substances, selecting components and enclosures that can withstand these conditions.
Panel Enclosure
Selection of an appropriate enclosure (NEMA or IP rated) based on the environmental conditions to protect the panel from external elements such as water, dust, and chemicals.
Assembly and Wiring
Skilled technicians assemble the electrical panel, following the design specifications. Wiring is carefully executed to ensure proper connections, reduce electromagnetic interference, and maintain electrical integrity.
Documentation
Comprehensive documentation, including operation manuals, maintenance procedures, and as-built drawings, is prepared for future reference.
Commissioning of New Sub Stations
The commissioning of new substations in industrial and mining settings involves the systematic process of verifying, testing, and bringing into operation the various components and systems within a newly constructed or upgraded electrical substation.
Substations play a crucial role in power distribution, transforming and managing electrical voltage levels to facilitate the safe and efficient supply of electricity to various equipment and machinery within an industrial or mining facility. The commissioning process is a critical step in ensuring the reliable and safe operation of a new substation.
It requires close collaboration between engineers, technicians, and project managers to systematically validate and verify the performance of the substation components before it is put into regular operation.
Key aspects of industrial and mining electrical panel repair and refurbishment include
Pre-Commissioning Planning
Develop a comprehensive commissioning plan outlining the scope, sequence of activities, and testing procedures. This plan is often prepared well in advance of the actual commissioning.
Functional Testing
Perform functional testing of individual components and systems to ensure they operate as intended. This includes checking the functionality of protection relays, control systems, and communication interfaces.
Voltage and Current Checks
Verify that the voltage and current levels at different points within the substation align with design specifications.
Control System Verification
Check the operation of the control system, including local and remote-control features. Verify communication links and interfaces with other systems.
Switchgear and Circuit Breaker Testing
Test the switching equipment, including circuit breakers and switchgear, to verify their reliability and ability to interrupt and isolate circuits when necessary.
Emergency Systems Testing
Test emergency systems, backup power supplies, and auxiliary systems to ensure their readiness in case of power outages or other emergencies.
Training
Provide training for operating and maintenance personnel on the operation, monitoring, and maintenance of the new substation.
Commissioning Report
Prepare a detailed commissioning report documenting the entire process, test results, and any issues addressed during commissioning.
Equipment Inspection
Conduct a thorough inspection of all substation components, including transformers, circuit breakers, switches, relays, meters, and control systems. Verify the equipment meets design specifications & industry standards.
Electrical Testing
Conduct electrical tests to verify the integrity and performance of the substation. This may include insulation resistance tests, continuity tests, and high-potential (Hi-Pot) tests.
Protection System Testing
Test the protection and relay systems to ensure they respond appropriately to abnormal conditions, such as overcurrent or fault events.
Transformer Testing
Perform specific tests on transformers, including turns ratio tests, impedance tests, and load tests, to ensure their proper functioning and efficiency.
Protection Coordination
Verify that the protection settings and coordination between protection devices are correctly configured to provide selective tripping and minimize the impact of faults.
Documentation and As-Built Drawings
Review and update documentation, including as-built drawings, to reflect any changes made during construction or commissioning.
Safety Checks
Conduct safety checks to ensure that all safety features, signage, and emergency procedures are in place and functional.
Commissioning of New Sub Stations
The commissioning of new substations in industrial and mining settings involves the systematic process of verifying, testing, and bringing into operation the various components and systems within a newly constructed or upgraded electrical substation.
Substations play a crucial role in power distribution, transforming and managing electrical voltage levels to facilitate the safe and efficient supply of electricity to various equipment and machinery within an industrial or mining facility. The commissioning process is a critical step in ensuring the reliable and safe operation of a new substation.
It requires close collaboration between engineers, technicians, and project managers to systematically validate and verify the performance of the substation components before it is put into regular operation.
Key aspects of industrial and mining electrical panel repair and refurbishment include
Pre-Commissioning Planning
Develop a comprehensive commissioning plan outlining the scope, sequence of activities, and testing procedures. This plan is often prepared well in advance of the actual commissioning.
Functional Testing
Perform functional testing of individual components and systems to ensure they operate as intended. This includes checking the functionality of protection relays, control systems, and communication interfaces.
Voltage and Current Checks
Verify that the voltage and current levels at different points within the substation align with design specifications.
Control System Verification
Check the operation of the control system, including local and remote-control features. Verify communication links and interfaces with other systems.
Switchgear and Circuit Breaker Testing
Test the switching equipment, including circuit breakers and switchgear, to verify their reliability and ability to interrupt and isolate circuits when necessary.
Emergency Systems Testing
Test emergency systems, backup power supplies, and auxiliary systems to ensure their readiness in case of power outages or other emergencies.
Training
Provide training for operating and maintenance personnel on the operation, monitoring, and maintenance of the new substation.
Commissioning Report
Prepare a detailed commissioning report documenting the entire process, test results, and any issues addressed during commissioning.
Equipment Inspection
Conduct a thorough inspection of all substation components, including transformers, circuit breakers, switches, relays, meters, and control systems. Verify the equipment meets design specifications & industry standards.
Electrical Testing
Conduct electrical tests to verify the integrity and performance of the substation. This may include insulation resistance tests, continuity tests, and high-potential (Hi-Pot) tests.
Protection System Testing
Test the protection and relay systems to ensure they respond appropriately to abnormal conditions, such as overcurrent or fault events.
Transformer Testing
Perform specific tests on transformers, including turns ratio tests, impedance tests, and load tests, to ensure their proper functioning and efficiency.
Protection Coordination
Verify that the protection settings and coordination between protection devices are correctly configured to provide selective tripping and minimize the impact of faults.
Documentation and As-Built Drawings
Review and update documentation, including as-built drawings, to reflect any changes made during construction or commissioning.
Safety Checks
Conduct safety checks to ensure that all safety features, signage, and emergency procedures are in place and functional.
Boilermaking
Boilermaking within the industrial and mining sectors involves the fabrication, assembly, installation, and maintenance of boilers and pressure vessels. Boilers are essential components in various industrial processes, including mining operations, where they are used to generate steam for heating, power generation, and other applications.
Boilermaking encompasses a range of skills and activities related to the construction and maintenance of these pressure vessels, ensuring their safety, efficiency, and compliance with industry standards. Boilermaking is a specialized field that requires skilled craftsmen, welders, and engineers who understand the intricacies of pressure vessel construction.
The reliability and safety of boilers are crucial for the overall functioning of industrial and mining processes. As such, boilermakers play a vital role in ensuring that these critical components are designed, fabricated, and maintained to the highest standards of quality and safety.
Key aspects of boilermaking within the industrial and mining sector include
Boiler Fabrication
Fabricating and assembling boilers and pressure vessels according to engineering specifications, design drawings, and applicable codes and standards.
Welding and Joining
Utilizing various welding techniques to join boiler components securely. Skilled welders play a crucial role in ensuring the integrity of the pressure vessel.
Pressure Testing
Conducting pressure tests to ensure the structural integrity and safety of the boiler. This involves testing the vessel under various pressure conditions to simulate operating conditions.
Maintenance and Repairs
Performing routine maintenance to ensure boilers operate efficiently and safely. Conducting repairs, replacements, or upgrades to address wear and tear, corrosion, or other issues.
Documentation
Maintaining accurate documentation, including fabrication records, inspection reports, and as-built drawings for each boiler or pressure vessel.
Alignment with Industry Standards
Staying updated on industry best practices, technological advancements, and changes in standards related to boilermaking.
Material Selection
Choosing appropriate materials for constructing boilers based on factors such as pressure, temperature, and the specific requirements of the industrial or mining process.
Quality Control
Implementing rigorous quality control measures throughout the fabrication process to detect and address any defects or deviations from design specifications.
Compliance with Regulations
Ensuring that boilermaking activities comply with local, national, and international regulations and standards, including boiler and pressure vessel codes.
Safety Measures
Implementing safety measures during fabrication, installation, and maintenance to protect workers and prevent accidents. Adhering to safety protocols and guidelines for working with high-pressure equipment.
Installation and Assembly
Installing boilers within industrial or mining facilities, connecting them to the necessary piping, control systems, and other auxiliary equipment.
Lamp Room Repairs
Lamp Room is a designated facility where workers obtain, store, and maintain their personal safety lamps or cap lamps. These lamps are crucial for providing illumination in underground or low-light environments commonly found in mining operations.
Lamp Room repairs within the industrial and mining sector involve the maintenance, servicing, and repair of these safety lamps to ensure they function effectively, providing reliable light sources for miners as they work in challenging conditions. Lamp Room repairs are critical for ensuring that miners have reliable and functional lighting equipment, which is vital for their safety in underground or confined spaces.
A well-maintained Lamp Room contributes significantly to the overall safety and efficiency of mining operations, helping to prevent accidents and ensuring that miners can effectively carry out their tasks in areas with limited natural light.
Key aspects of Lamp Room repairs in the industrial and mining sector include
Inspection and Maintenance
Regular inspection of safety lamps to identify any signs of wear, damage, or malfunction. Cleaning and routine maintenance to ensure lamps are in optimal working condition.
Casing and Housing Inspection
Inspecting the casing and housing of lamps for any cracks, breaks, or damage. Repairing or replacing damaged casings to maintain the structural integrity of the lamp.
Sealing and Waterproofing
Ensuring that lamps are properly sealed and waterproofed, especially if they are used in wet or damp underground environments.
Record Keeping
Maintaining detailed records of lamp inspections, repairs, and replacements. Keeping track of the service history of each safety lamp.
Training and Education
Providing training to miners on the proper use, care, and maintenance of their safety lamps. Educating miners on the importance of reporting any issues with their lamps promptly.
Switches and Controls
Verifying the functionality of switches and controls to ensure miners can easily operate the lamps in various conditions. Repairing or replacing switches if they are faulty.
Compliance with Safety Standards
Conducting repairs to ensure that safety lamps comply with relevant safety standards and regulations. Performing tests to ensure luminosity and other safety features meet required specifications.
Battery and Power Source Checks
Verifying the functionality of the power source, which may include rechargeable batteries, to ensure a continuous and reliable power supply.
Charging Systems
Checking and maintaining charging systems to ensure lamps are ready for use and adequately charged before each shift.
Bulb Replacement
Replacing light bulbs or LEDs to maintain appropriate brightness levels.
Lamp Room Repairs
Lamp Room is a designated facility where workers obtain, store, and maintain their personal safety lamps or cap lamps. These lamps are crucial for providing illumination in underground or low-light environments commonly found in mining operations.
Lamp Room repairs within the industrial and mining sector involve the maintenance, servicing, and repair of these safety lamps to ensure they function effectively, providing reliable light sources for miners as they work in challenging conditions. Lamp Room repairs are critical for ensuring that miners have reliable and functional lighting equipment, which is vital for their safety in underground or confined spaces.
A well-maintained Lamp Room contributes significantly to the overall safety and efficiency of mining operations, helping to prevent accidents and ensuring that miners can effectively carry out their tasks in areas with limited natural light.
Key aspects of Lamp Room repairs in the industrial and mining sector include
Inspection and Maintenance
Regular inspection of safety lamps to identify any signs of wear, damage, or malfunction. Cleaning and routine maintenance to ensure lamps are in optimal working condition.
Casing and Housing Inspection
Inspecting the casing and housing of lamps for any cracks, breaks, or damage. Repairing or replacing damaged casings to maintain the structural integrity of the lamp.
Sealing and Waterproofing
Ensuring that lamps are properly sealed and waterproofed, especially if they are used in wet or damp underground environments.
Record Keeping
Maintaining detailed records of lamp inspections, repairs, and replacements. Keeping track of the service history of each safety lamp.
Training and Education
Providing training to miners on the proper use, care, and maintenance of their safety lamps. Educating miners on the importance of reporting any issues with their lamps promptly.
Switches and Controls
Verifying the functionality of switches and controls to ensure miners can easily operate the lamps in various conditions. Repairing or replacing switches if they are faulty.
Compliance with Safety Standards
Conducting repairs to ensure that safety lamps comply with relevant safety standards and regulations. Performing tests to ensure luminosity and other safety features meet required specifications.
Battery and Power Source Checks
Verifying the functionality of the power source, which may include rechargeable batteries, to ensure a continuous and reliable power supply.
Charging Systems
Checking and maintaining charging systems to ensure lamps are ready for use and adequately charged before each shift.
Bulb Replacement
Replacing light bulbs or LEDs to maintain appropriate brightness levels.
Boilermaking
Boilermaking within the industrial and mining sectors involves the fabrication, assembly, installation, and maintenance of boilers and pressure vessels. Boilers are essential components in various industrial processes, including mining operations, where they are used to generate steam for heating, power generation, and other applications.
Boilermaking encompasses a range of skills and activities related to the construction and maintenance of these pressure vessels, ensuring their safety, efficiency, and compliance with industry standards. Boilermaking is a specialized field that requires skilled craftsmen, welders, and engineers who understand the intricacies of pressure vessel construction.
The reliability and safety of boilers are crucial for the overall functioning of industrial and mining processes. As such, boilermakers play a vital role in ensuring that these critical components are designed, fabricated, and maintained to the highest standards of quality and safety.
Key aspects of boilermaking within the industrial and mining sector include
Boiler Fabrication
Fabricating and assembling boilers and pressure vessels according to engineering specifications, design drawings, and applicable codes and standards.
Welding and Joining
Utilizing various welding techniques to join boiler components securely. Skilled welders play a crucial role in ensuring the integrity of the pressure vessel.
Pressure Testing
Conducting pressure tests to ensure the structural integrity and safety of the boiler. This involves testing the vessel under various pressure conditions to simulate operating conditions.
Maintenance and Repairs
Performing routine maintenance to ensure boilers operate efficiently and safely. Conducting repairs, replacements, or upgrades to address wear and tear, corrosion, or other issues.
Documentation
Maintaining accurate documentation, including fabrication records, inspection reports, and as-built drawings for each boiler or pressure vessel.
Alignment with Industry Standards
Staying updated on industry best practices, technological advancements, and changes in standards related to boilermaking.
Material Selection
Choosing appropriate materials for constructing boilers based on factors such as pressure, temperature, and the specific requirements of the industrial or mining process.
Quality Control
Implementing rigorous quality control measures throughout the fabrication process to detect and address any defects or deviations from design specifications.
Compliance with Regulations
Ensuring that boilermaking activities comply with local, national, and international regulations and standards, including boiler and pressure vessel codes.
Safety Measures
Implementing safety measures during fabrication, installation, and maintenance to protect workers and prevent accidents. Adhering to safety protocols and guidelines for working with high-pressure equipment.
Installation and Assembly
Installing boilers within industrial or mining facilities, connecting them to the necessary piping, control systems, and other auxiliary equipment.
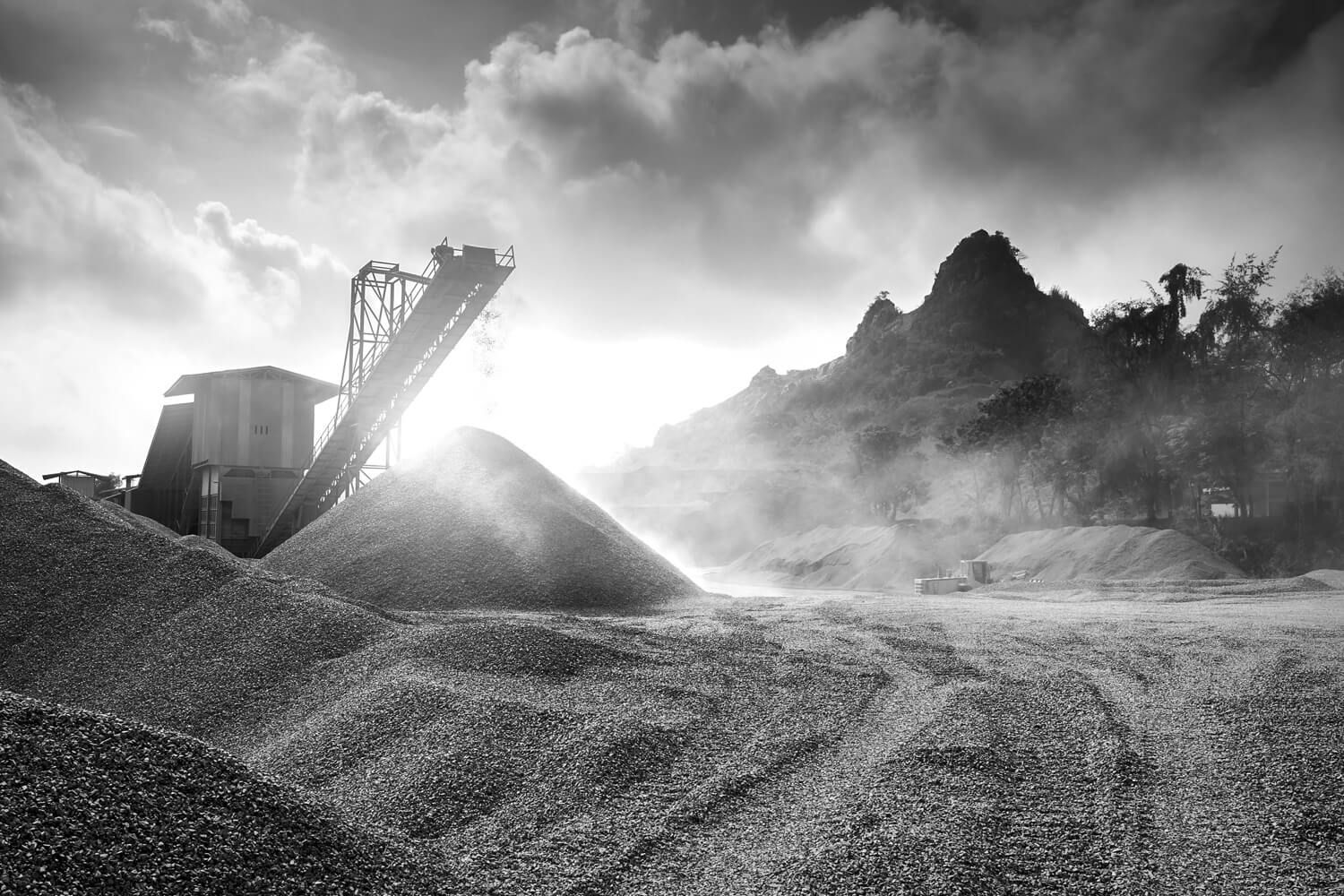
Engineering Solutions
Engineering solutions within the industrial and mining sector involve the application of engineering principles, technologies, and methodologies to address challenges, improve processes, and optimize operations in industrial and mining environments. These solutions aim to enhance efficiency, safety, sustainability, and overall performance while addressing specific needs and constraints within the industrial and mining sectors.
Engineering solutions in the industrial and mining sector are interdisciplinary and often involve collaboration between engineers, scientists, technicians, and other professionals. These solutions aim to address complex challenges and contribute to the sustainable and responsible development of industrial and mining operations.
Key aspects of engineering solutions within the industrial and mining sector include
Process Optimization
Analyzing and improving existing industrial and mining processes to increase efficiency, reduce costs, and enhance overall productivity.
Safety Engineering
Implementing engineering solutions to enhance safety protocols, risk assessments, and emergency response plans within industrial and mining settings. This may involve designing safety systems, barriers, and implementing technologies to mitigate risks.
Environmental Compliance
Designing and implementing engineering solutions to ensure compliance with environmental regulations. This includes waste management, emissions control, and sustainable practices to minimize the environmental impact of industrial and mining activities.
Materials Handling and Logistics
Developing solutions for efficient materials handling, transportation, and logistics within industrial and mining operations. This includes optimizing supply chain processes and designing conveyor systems, material transport vehicles, and storage solutions.
Equipment Design and Innovation
Designing new machinery and equipment or optimizing existing ones to meet specific industrial or mining requirements. This includes incorporating advanced technologies for automation, control, and monitoring.
Water and Waste Management
Designing solutions for effective water management, wastewater treatment, and waste disposal in industrial and mining contexts. This involves addressing environmental regulations and minimizing the impact on local ecosystems.
Regulatory Compliance
Ensuring that engineering solutions align with local and international regulations, standards, and industry best practices.
Energy Efficiency
Developing solutions to optimize energy consumption, reduce waste, and increase energy efficiency in industrial and mining processes. This may include the implementation of energy-efficient technologies and renewable energy sources.
Automation and Control Systems
Designing and implementing automation solutions, control systems, and instrumentation to improve the precision, reliability, and efficiency of industrial and mining processes. This may involve the integration of sensors, actuators, and advanced control algorithms.
Data Analytics and Decision Support
Leveraging data analytics and information systems to gather, analyze, and interpret data for decision-making. This includes implementing solutions for predictive maintenance, process optimization, and real-time monitoring.
Infrastructure Design and Maintenance
Designing and maintaining industrial and mining infrastructure, including buildings, roads, bridges, and utilities. This involves considerations for structural integrity, durability, and compliance with industry standards.
Mine Planning and Resource Management
Developing engineering solutions for mine planning, resource extraction, and mineral processing. This includes optimizing extraction methods, designing mining equipment, and managing resource sustainability.
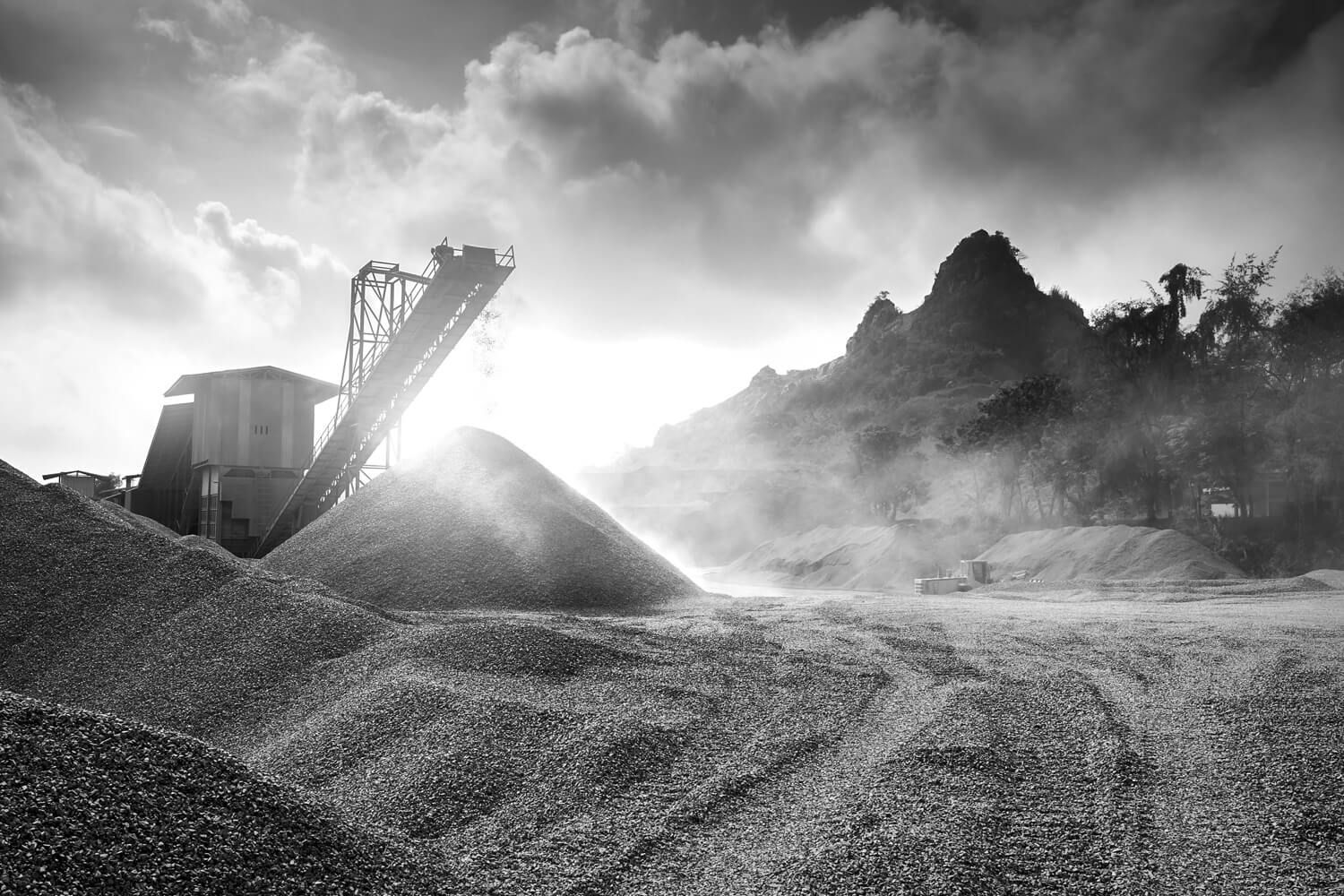
Engineering Solutions
Engineering solutions within the industrial and mining sector involve the application of engineering principles, technologies, and methodologies to address challenges, improve processes, and optimize operations in industrial and mining environments. These solutions aim to enhance efficiency, safety, sustainability, and overall performance while addressing specific needs and constraints within the industrial and mining sectors.
Engineering solutions in the industrial and mining sector are interdisciplinary and often involve collaboration between engineers, scientists, technicians, and other professionals. These solutions aim to address complex challenges and contribute to the sustainable and responsible development of industrial and mining operations.
Key aspects of engineering solutions within the industrial and mining sector include
Process Optimization
Analyzing and improving existing industrial and mining processes to increase efficiency, reduce costs, and enhance overall productivity.
Safety Engineering
Implementing engineering solutions to enhance safety protocols, risk assessments, and emergency response plans within industrial and mining settings. This may involve designing safety systems, barriers, and implementing technologies to mitigate risks.
Environmental Compliance
Designing and implementing engineering solutions to ensure compliance with environmental regulations. This includes waste management, emissions control, and sustainable practices to minimize the environmental impact of industrial and mining activities.
Materials Handling and Logistics
Developing solutions for efficient materials handling, transportation, and logistics within industrial and mining operations. This includes optimizing supply chain processes and designing conveyor systems, material transport vehicles, and storage solutions.
Equipment Design and Innovation
Designing new machinery and equipment or optimizing existing ones to meet specific industrial or mining requirements. This includes incorporating advanced technologies for automation, control, and monitoring.
Water and Waste Management
Designing solutions for effective water management, wastewater treatment, and waste disposal in industrial and mining contexts. This involves addressing environmental regulations and minimizing the impact on local ecosystems.
Regulatory Compliance
Ensuring that engineering solutions align with local and international regulations, standards, and industry best practices.
Energy Efficiency
Developing solutions to optimize energy consumption, reduce waste, and increase energy efficiency in industrial and mining processes. This may include the implementation of energy-efficient technologies and renewable energy sources.
Automation and Control Systems
Designing and implementing automation solutions, control systems, and instrumentation to improve the precision, reliability, and efficiency of industrial and mining processes. This may involve the integration of sensors, actuators, and advanced control algorithms.
Data Analytics and Decision Support
Leveraging data analytics and information systems to gather, analyze, and interpret data for decision-making. This includes implementing solutions for predictive maintenance, process optimization, and real-time monitoring.
Infrastructure Design and Maintenance
Designing and maintaining industrial and mining infrastructure, including buildings, roads, bridges, and utilities. This involves considerations for structural integrity, durability, and compliance with industry standards.
Mine Planning and Resource Management
Developing engineering solutions for mine planning, resource extraction, and mineral processing. This includes optimizing extraction methods, designing mining equipment, and managing resource sustainability.
Manufacturing
Our manufacturing division encompasses the design, production, and supply of high-quality electrical, mechanical, and industrial equipment tailored specifically for the mining and industrial sectors.
Electrical Tool Bag
Mechanical Tool Trolley
Electrical and Mechanical Tool Kits
Electrical Panels
Electrical Screwdrivers
Construction
We specialise in delivering high-quality construction and installation services, tailored to the industrial construction sector. With a focus on innovation and efficiency, this division provides comprehensive solutions, including design, installation, and maintenance.
Our team of experienced professionals ensures that every project meets rigorous safety and performance standards, contributing to reliable and sustainable operation of industrial facilities. Through a commitment of excellence and customer satisfaction, our construction division has established itself as a trusted partner in the industry.
Manufacturing Plant Construction: Design and construction of state-of-the-art manufacturing facilities.
Warehouse and Distribution Centers: Building large-scale warehouses and logistics facilities.
Heavy Industrial Facilities: Constructing factories and industrial complexes.
Project Management: Comprehensive management from planning through to project completion.
Manufacturing
Our manufacturing division encompasses the design, production, and supply of high-quality electrical, mechanical, and industrial equipment tailored specifically for the mining and industrial sectors.
Electrical Tool Bag
Mechanical Tool Trolley
Electrical and Mechanical Tool Kits
Electrical Panels
Electrical Screwdrivers
Construction
We specialise in delivering high-quality construction and installation services, tailored to the industrial construction sector. With a focus on innovation and efficiency, this division provides comprehensive solutions, including design, installation, and maintenance.
Our team of experienced professionals ensures that every project meets rigorous safety and performance standards, contributing to reliable and sustainable operation of industrial facilities. Through a commitment of excellence and customer satisfaction, our construction division has established itself as a trusted partner in the industry.
Manufacturing Plant Construction: Design and construction of state-of-the-art manufacturing facilities.
Warehouse and Distribution Centers: Building large-scale warehouses and logistics facilities.
Heavy Industrial Facilities: Constructing factories and industrial complexes.
Project Management: Comprehensive management from planning through to project completion.